Description
The Miller Continuum Feeder (Dual) is an advanced industrial wire feeder. With Tru - Feed™ technology, it boosts productivity by enhancing weld quality, offering ease of use, and providing system flexibility. It's designed to work perfectly with a Continuum power source.
New low - inertia motor
It offers a quicker response, ensuring the best arc starts with minimal spatter.
Balanced - pressure drive - roll design and tensioners
Feeds wire in the truest and straightest way, improving feedability and welding performance.
Spring - loaded Accu - Mate™ connection
Aligns the gun precisely in the drive - roll carrier, preventing it from coming loose and providing consistent wire feeding.
Quick - change dual - bearing drive rolls
Deliver more consistent wire feeding.
Drive rolls and guides
These are common with other Miller industrial feeders, so you can use existing parts. The inlet guide can be installed without tools.
Tool - less positive - locking rotatable drive assembly
Allows operators to rotate the drive, eliminating sharp bends in the wire feed path. This extends the gun - liner life and helps feed difficult wires.
Specifications
Click the image below to view the full spec sheet.
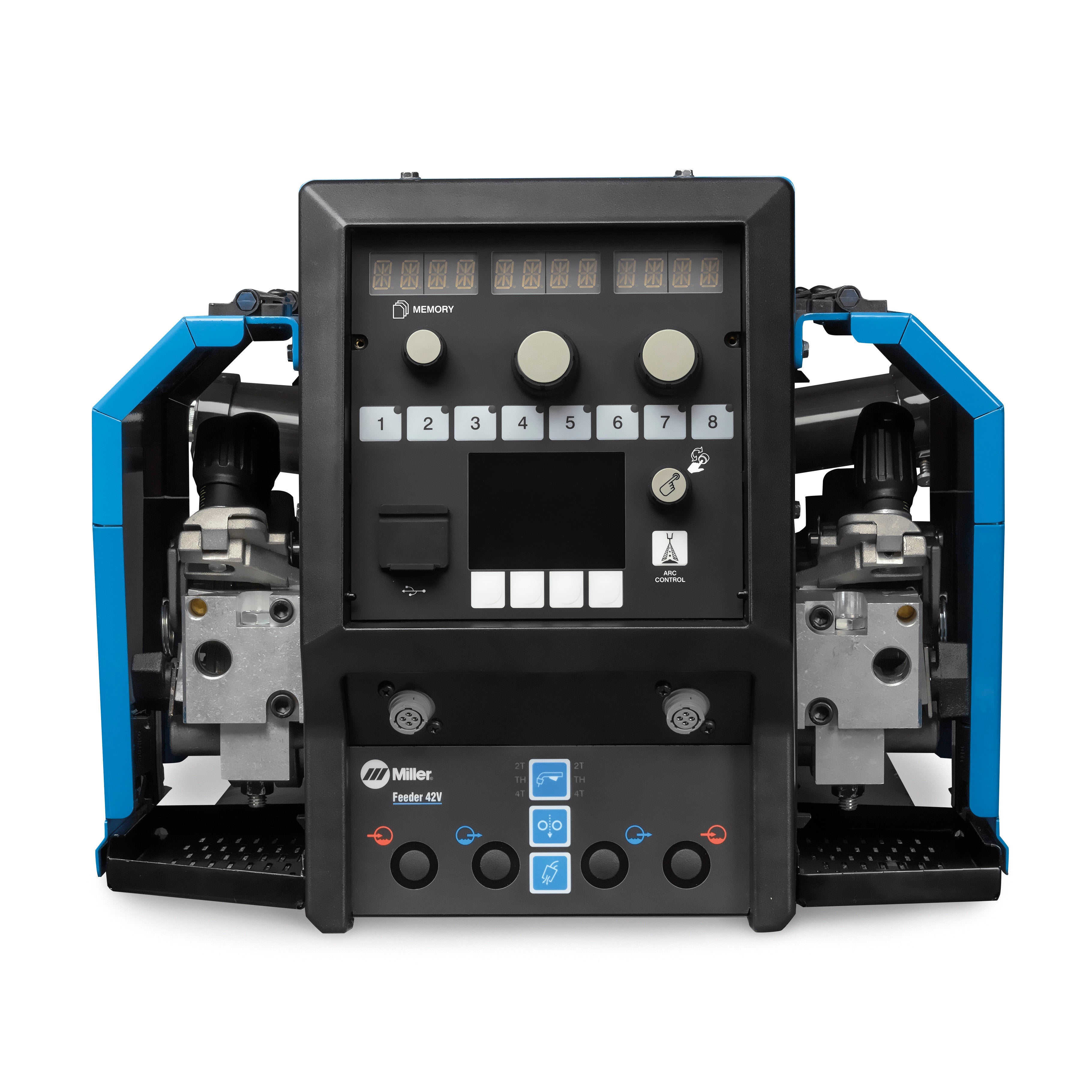
Using the Miller Continuum Feeder (Dual) is straightforward. First, make sure it's connected to a Continuum power source. When starting the welding process, the new low - inertia motor will quickly respond, giving you a great arc start with little spatter. The balanced - pressure drive - roll design and tensioners will ensure the wire is fed straight and true for better welding. The spring - loaded Accu - Mate™ connection keeps the gun in place for consistent wire feeding. You can easily change the quick - change dual - bearing drive rolls for continued consistent feeding. And don't worry about parts; the drive rolls and guides are common with other Miller industrial feeders, and you can install the inlet guide without tools. If you need to adjust the wire feed path, use the tool - less positive - locking rotatable drive assembly to rotate the drive and avoid sharp bends. As for maintenance, keep the feeder clean from dust and debris. Check the drive rolls and guides regularly for wear and replace them if needed. Also, make sure the connections are tight to ensure proper operation.